Home > FAQs
Home > FAQs
FAQs
Flexible Couplings
Composite Disc (CD®) Couplings
Where should I use a Single-Flex versus a Double-Flex CD Coupling?
A Single-Flex CD Coupling can be used where parallel misalignment is minimal. The Single-Flex CD Coupling can be ideal in these situations, such as many servomotor and automation equipment applications, where the shafts are typically well aligned. With only one disc-pack, the Single-Flex CD Coupling offers a more compact size, higher torsional stiffness, lower inertia, yet it can still handle any inevitable small amounts of parallel misalignment that may exist. Both the Single-Flex and Double-Flex CD Couplings handle up to 3° of angular misalignment.
A Double-Flex CD Coupling has two disc-packs, which allows it to handle a much greater amount of parallel misalignment. Also, by using two open-arm disc-packs, the design of the Double-Flex CD Coupling greatly reduces the reaction loads on the connected equipment.
Other than the misalignment capacities, in some cases the DBSE (distance between shaft ends) will determine whether you should use the shorter Single-Flex or the longer Double-Flex Solution. Floating Shaft CD Couplings should be considered in very large DBSE applications.
A Double-Flex CD Coupling has two disc-packs, which allows it to handle a much greater amount of parallel misalignment. Also, by using two open-arm disc-packs, the design of the Double-Flex CD Coupling greatly reduces the reaction loads on the connected equipment.
Other than the misalignment capacities, in some cases the DBSE (distance between shaft ends) will determine whether you should use the shorter Single-Flex or the longer Double-Flex Solution. Floating Shaft CD Couplings should be considered in very large DBSE applications.
Why is there a continuous and a peak torque rating listed in the specifications?
The continuous torque rating for a CD Coupling is a torque the coupling can operate at for normal operating conditions (24/7/365). The peak torque rating for a CD Coupling is for intermittent torque spikes (start-up, e-stop, etc.) that may occur infrequently. Exceeding the continuous torque rating of a CD coupling on a frequent basis will shorten the life of the coupling.
What if I have an extended distance between my prime mover and my driven load?
Zero-Max offers custom designs as well as a full line of Floating Shaft CD Couplings that can be made to accommodate longer distances between the shaft ends (DBSE). Depending on the speed and torque of the application, spans of up to 15 feet or more can be accommodated. Please reference our online catalog, website, or contact the factory for details.
What is the minimum shaft engagement on a CD Coupling with clamping hubs?
Ideally, the shaft will engage the entire length of the hub (dimension “B” in catalog). The shaft can extend past the hub end into the disc-pack area as long as it does not come in contact with the disc-pack (check disc diameter dimension “H” in catalog) or the mating shaft or hub. If the shaft cannot engage the full length of the hub, it must still engage through the entire flexing area of the hub for full torque transmission. This distance is approximately 2/3 - 3/4 of the overall hub length, depending on the size of the coupling. Please contact the factory if you have any questions.
Does Zero-Max manufacture larger couplings than are shown in the catalog?
Yes. Zero-Max has successfully manufactured special coupling designs for higher torque applications than what are shown in our catalog. As one example, we manufacture couplings for Wind Turbines that generate up to 2 MW of power and 33 kNm of torque. Please contact the factory with your application requirements to review larger coupling designs and right-size the coupling for your application.
What are the standard keyway sizes?
The standard keyway sizes are based on AGMA and ISO standards.Please refer to the CD Coupling catalog for a table that lists all standard keyway sizes.Non-standard keyway sizes are also available. Contact the factory for further details.
Can I get custom bores or keyways?
Yes. Any inch bore sizes that fall on a 1/16” increments and metric bore sizes that fall on a whole millimeter increments are standard for CD Couplings. Zero-Max also offers custom bore sizes, as well as splined or tapered bores to meet the needs of your application. Additionally, Zero-Max can manufacture non-standard keyways as well as custom tolerance bores and keyways to meet specific dimensional requirements.
What if I have a higher speed application?
The CD Coupling catalog lists a maximum RPM specification for the various coupling sizes, models, and hub styles. This is a general speed specification that applies to most applications. If your RPM is approaching or exceeding the value listed, contact the factory to discuss your specific application. We will review your application and help determine if a standard CD Coupling will work or help design a special that will. Factors that may be considered for higher-speed operation include dynamic balancing, reducing misalignment, and/or a review of the lifetime requirements.
Can Zero-Max dynamic balance my CD Coupling?
Yes, we can add dynamic balancing to the CD Couplings as needed for applications. Typically, higher speed applications or equipment that is sensitive to vibrations (i.e. test equipment) may benefit from being dynamically balanced. Zero-Max has the technology required to do most coupling balancing jobs in-house, allowing us to offer an economical option with a faster turnaround.
Why consider using an A1C versus an AC style hub?
Both the A1C and AC feature aluminum construction with clamp-style hubs that are available with or without a keyway. However, each style offers its own advantages.
The A1C style hub features an integrated clamping hub that provides the capability to handle the coupling’s peak torque rating for any bore size offered without the need for a key. This design also offers larger bore size capacities compared to the AC style hubs and typically has faster Delivery.
The AC style hub is dimensionally identical to the steel clamp-style hub, but it offers a lower weight and inertia advantage due to the use of the lighter weight aluminum material. Like the steel clamp-style hub, this design has a separate shaft collar which results in a smaller bore size capacity compared to the A1C style hubs and may require a key to handle the coupling’s peak torque rating. Contact the factory for further details.
The A1C style hub features an integrated clamping hub that provides the capability to handle the coupling’s peak torque rating for any bore size offered without the need for a key. This design also offers larger bore size capacities compared to the AC style hubs and typically has faster Delivery.
The AC style hub is dimensionally identical to the steel clamp-style hub, but it offers a lower weight and inertia advantage due to the use of the lighter weight aluminum material. Like the steel clamp-style hub, this design has a separate shaft collar which results in a smaller bore size capacity compared to the A1C style hubs and may require a key to handle the coupling’s peak torque rating. Contact the factory for further details.
Can my CD Coupling support a radial load?
The Single-Flex CD Coupling can support a limited amount of radial load. Please contact the factory for assistance in sizing the coupling if your application requires supporting a radial load.
Can the CD Coupling be used in vertical applications?
Yes. The CD Coupling can be used to connect shafts that are oriented vertically. If using a Floating Shaft CD Coupling in a vertical oriented application, please contact the factory with the speed, torque, misalignment, and DBSE (distance between shaft ends) of your application to confirm sizing.
Is there any maintenance required for my CD Coupling?
There are no scheduled maintenance intervals for the CD Couplings, and many of our CD Couplings run indefinitely in the application. However, any jam-ups, overloads, or crashes on the equipment may require replacement of the disc packs. It is also recommended to re-torque the disc pack bolts after several hours of operation following installation, where possible.
When installing or re-torquing the bolts, it is critical that the disc-pack bolts be torqued-to-spec per the Installation Instructions. This is essential for proper operation and long life of the coupling. The Instructions, including the recommended tightening torques, can be found under the “Downloads” section of our website.
Preventive maintenance considerations would involve periodically visually inspecting the coupling when the machine is shut down. Things to look for include anything abnormal, such as obviously loose bolts, or any delamination of the disc pack. Note that if there is any delamination showing, it does not mean the disc pack will imminently fail; however, it would be best practice to replace the disc-pack at the next opportunity.
When installing or re-torquing the bolts, it is critical that the disc-pack bolts be torqued-to-spec per the Installation Instructions. This is essential for proper operation and long life of the coupling. The Instructions, including the recommended tightening torques, can be found under the “Downloads” section of our website.
Preventive maintenance considerations would involve periodically visually inspecting the coupling when the machine is shut down. Things to look for include anything abnormal, such as obviously loose bolts, or any delamination of the disc pack. Note that if there is any delamination showing, it does not mean the disc pack will imminently fail; however, it would be best practice to replace the disc-pack at the next opportunity.
Can I replace disc packs in the field?
Yes. CD disc-packs are easily replaced in the field. In most cases, our coupling design offers disc packs that are a drop-out design, meaning you do not need to move the hubs to replace disc packs. The disc pack is also a unitized design, making it easier to handle for removing the old one and installing a new one. Coupling concentricity after disc pack replacement is also ensured by the design of the CD Coupling. Full disc-pack replacement instructions can be found under the “Downloads” section on our website.
What is the minimum order quantity for special versions of the CD Coupling?
There is no minimum quantity for special design couplings. We often design and build special designs for just 1-piece, but can also support custom designs that require 100s or 1000s of pieces. We are happy to discuss your application to understand the requirements and provide a custom design to fit the needs of the application. In almost all cases, there are no upfront Engineering fees involved. Please call to discuss if you need a special design for your application.
Why choose a CD Coupling versus a ServoClass Coupling, or vice versa?
In many cases, the size of coupling needed for the application will determine where a CD Coupling or ServoClass Coupling is a better fit. In general, the size range of the ServoClass Couplings handle the smaller applications in terms of torque, load, and shaft sizes, while the size range of the CD Coupling will handle larger applications. There are several coupling sizes that overlap between the CD and ServoClass Couplings. In those cases, which series is a better fit will depend on the application and requirements such as misalignment, torque, torsional stiffness, vibration, shock, delivery, cost, and more. Contact the factory to discuss your specific requirements.
ServoClass® Couplings
Where should I use a Single-Flex (SC) versus a Double-Flex (SD) ServoClass Coupling?
Most applications will use the Double-Flex (SC) series of the ServoClass Coupling due to its misalignment capacity.The typical application for this is a 4-bearing system, as illustrated below:

With the 4 bearing systems, the shafts are fully supported and generally have some inevitable amount of misalignment and/or develop misalignment over time. The Double-Flex design readily accommodates any combination of parallel, angular, and axial misalignments and keeps reaction loads low on the connected components.
The Single-Flex (SD) series of the ServoClass Coupling is suited for use where support is needed for one shaft. The typical application for this is a 3 bearing “semi-floating shaft” application, as illustrated below:

The Single-Flex does not allow for parallel misalignment; however, it may also be used where a shorter length is required in an application with a very well piloted connection to eliminate parallel misalignment. Another use of the Single-Flex is to use two of them at either end of a customer-supplied shaft to make a Floating Shaft Coupling to accommodate a larger DBSE (distance between shaft ends).

With the 4 bearing systems, the shafts are fully supported and generally have some inevitable amount of misalignment and/or develop misalignment over time. The Double-Flex design readily accommodates any combination of parallel, angular, and axial misalignments and keeps reaction loads low on the connected components.
The Single-Flex (SD) series of the ServoClass Coupling is suited for use where support is needed for one shaft. The typical application for this is a 3 bearing “semi-floating shaft” application, as illustrated below:

The Single-Flex does not allow for parallel misalignment; however, it may also be used where a shorter length is required in an application with a very well piloted connection to eliminate parallel misalignment. Another use of the Single-Flex is to use two of them at either end of a customer-supplied shaft to make a Floating Shaft Coupling to accommodate a larger DBSE (distance between shaft ends).
Does Zero-Max provide a Floating Shaft version of the ServoClass Coupling?
No. Although a Floating Shaft is not available from the factory, many of our customers build their own Floating Shaft Coupling simply by using (2) Single Disc (SD) series couplings – one attached at each end to a customer-supplied intermediate shaft. This assembly arrangement offers a Floating Shaft Coupling to accommodate a larger DBSE (distance between shaft ends).
What is the maximum operating torque for the ServoClass Coupling?
The operating torque listed for the ServoClass Coupling is the maximum allowable torque for the coupling. Any peak torques or torque spikes anticipated in the application should be considered when sizing to the operating torque listed.
What is the minimum shaft engagement on a ServoClass Coupling hub?
Ideally, the shaft will engage the entire length of the hub (dimension “LB” in catalog). The shaft can also extend past the hub end into the disc-pack area as long as it does not come in contact with the disc-pack (check disc diameter dimension “K” in catalog) or the mating shaft or hub. If the shaft cannot engage the full length of the hub, it must still engage the entire flexing area of the hub for full torque transmission. This distance is approximately 2/3 - 3/4 of the overall hub length, depending on the size of the coupling. Please contact the factory if you have any questions.
Can I get a keyway on the hub bore?
Yes. Although the ServoClass Coupling is a keyless coupling in its standard form, keyways may be added per customer request at a nominal cost adder. Non-standard keyway sizes can also be accommodated in most cases.
Can I get custom bores or keyways?
Yes. Any inch bore sizes that fall on 1/16” increments and metric bore sizes that fall on a whole millimeter increments are standard for ServoClass Couplings. Zero-Max also offers custom bore sizes as well as non-standard keyways and custom tolerance bores and keyways to meet specific dimensional requirements.
Can I mount a non-keyed bore hub on a shaft with a keyway or flat?
Yes. The ServoClass Coupling hub can be mounted on a shaft with an empty keyway or a flat. The transmittable torque may be slightly reduced (due to the loss of the keyway/ flatted surface area for the clamp connection), but this is typically not a concern unless small bore sizes are used. Please contact the factory if you have any questions.
For optimal clamping force, we do recommend the keyway or flat is on the opposite side of the hub from the clamp screw. See diagram below for further details.
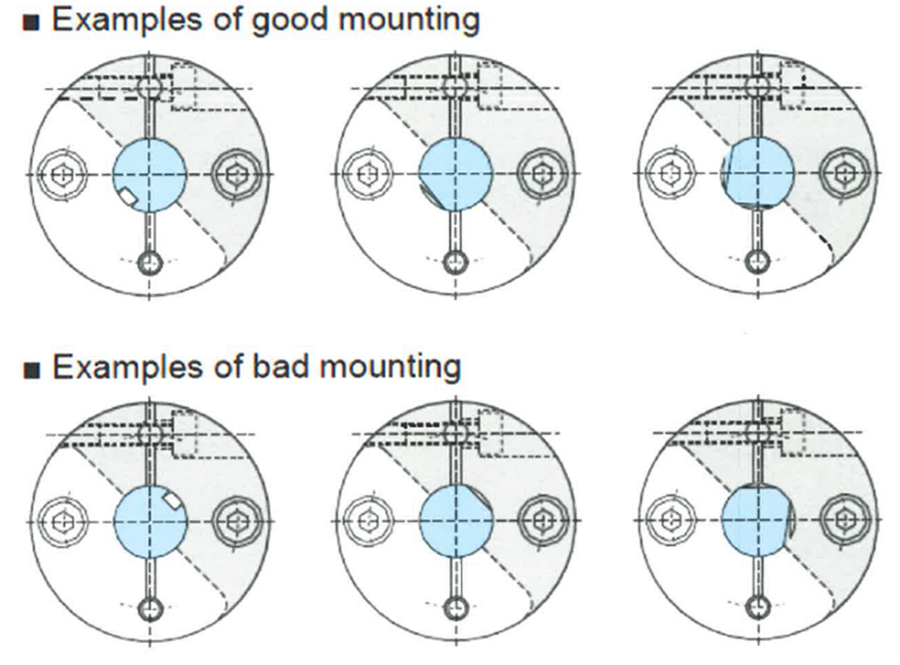
For optimal clamping force, we do recommend the keyway or flat is on the opposite side of the hub from the clamp screw. See diagram below for further details.
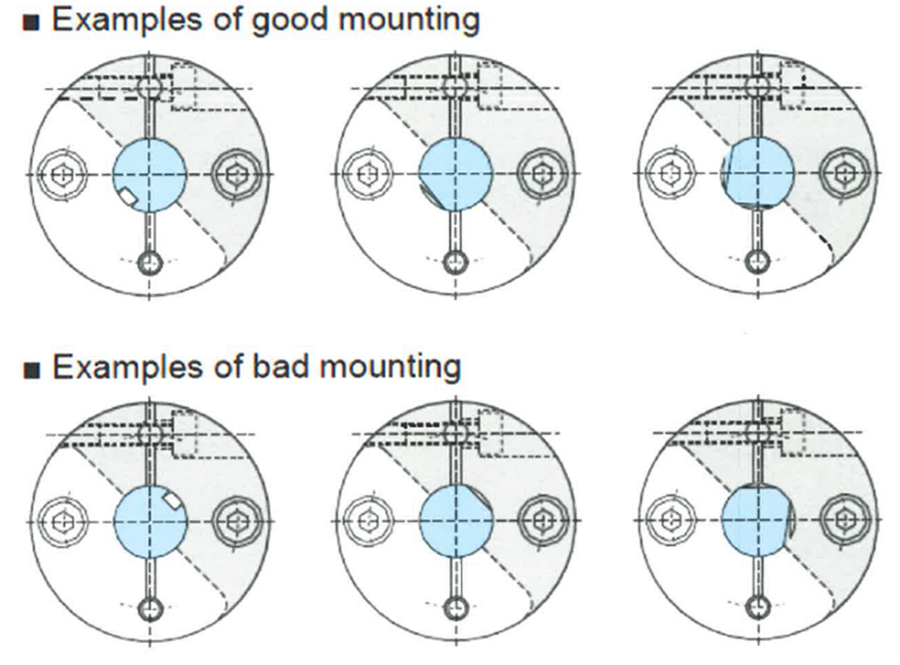
What if I have a tapered shaft in my application?
We offer tapered adaptors for some of the ServoClass Coupling sizes. The clamp-style hub itself does not allow for clamping onto the taper, however the tapered bore adaptor fits securely in the standard clamping hub bore and has an internal taper to secure it to the tapered shaft. The tapered adaptors have a 1:10 internal taper to match Fanuc servomotor shafts and other shafts having a 1:10 taper. The available tapered adaptor sizes are for an 11mm, 14mm, or 16mm major diameter of the taper.
Can I replace disc elements in the field?
No. Replacement discs are not available since the discs are not field-replaceable. Zero-Max uses purpose-built assembly fixtures at our factory to assemble ServoClass couplings with the concentricity required for optimal performance and life of the Coupling.
Can Zero-Max dynamic balance my ServoClass Coupling?
Yes. We can add dynamic balancing to the ServoClass Couplings as needed for applications. Typically, higher speed applications or equipment that is sensitive to vibrations (i.e. test equipment) may benefit from being dynamically balanced. Zero-Max has the technology required to do most coupling balancing jobs in-house, allowing us to offer an economical option with a faster turnaround.
Can I choose Style "A", "B", or "C" hub combination for my ServoClass Coupling?
No. The hub style combination used is based on the size of the coupling and the bore sizes required. Some ServoClass sizes have a reduced diameter hub for smaller bores that provides a higher clamping force to achieve optimal performance. Not all ServoClass Coupling sizes have a reduced diameter hub. The ServoClass Coupling sizes that have the reduced diameter hub are listed in the catalog, along with the range of bores that use this hub. Bore sizes larger than the maximum bore of the reduced diameter hub will utilize the standard diameter hub.
- Style "A" has (2) reduced diameter hubs
- Style "B" has (1) reduced diameter hub & (1) standard diameter hub
- Style "C" has (2) standard diameter hubs
Why choose a ServoClass Coupling versus a CD Coupling, or vice versa?
In most cases, the size of coupling needed for the application will determine where a ServoClass Coupling is used versus a CD Coupling. In general, the size range of the ServoClass Couplings handle the smaller applications in terms of torque, load, and shaft sizes, while the size range of the CD Coupling will handle larger applications. There are several coupling sizes that overlap between the ServoClass and CD Couplings. In those cases, which series is a better fit will depend on the application and requirements such as misalignment, torque, torsional stiffness, vibration, shock, delivery, cost, and more. Contact the factory to discuss your specific requirements.
Control-Flex Couplings
Why are Control-Flex Couplings good for Encoders, Tachometers, Resolvers, and other Instrumentation applications?
There are many reasons the Control-Flex Coupling provides exceptional value for encoder and other Instrumentation applications:
- A large minimum to maximum bore range is available. The large bore range helps to keep from oversizing the coupling where it is connected to a small diameter encoder shaft on one side, and a larger diameter machine shaft on the other side.
- Electrical Isolation is inherent in the design of the Control-Flex Couplings due to the construction of the flex member. This electrical isolation eliminates any stray electrical current from passing through the coupling and causing bearing issues in the encoder.
- Low reaction loads and a high misalignment capacity of the Control-Flex. The flex member design keeps the reaction loads minimal for the smaller encoder bearings, which provides longer life for the application, even under a misaligned condition.
- Zero-backlash. This is critical for maintaining positioning accuracy in instrumentation applications.
- Low inertia. This provides a fast and accurate response to acceleration and deceleration on the machine.
- Clamp-style hubs. This proven connection method maintains an effective, solid shaft connection during starting, stopping, reversing, etc. on the machine. This style of hub offers a stronger and more reliable shaft connection than a traditional setscrew design.
Can I get a keyway on the hub bore?
Yes. Although the Clamp-Style Control-Flex Coupling is a keyless coupling in its standard form, and keyways are not required for proper connection, keyways may be added per customer request at a nominal cost adder. Non-standard keyway sizes can also be accommodated in most cases. Also note that most Control-Flex Coupling applications tend to have lower torque requirements where the keyless hub can be clamped overtop an empty keyway and still provide ample transmittable torque.
Please Note: Bolted-Style Control-Flex Couplings utilize set-screw hubs with keyways. In this case, standard keyway sizes are based on AGMA standards, and the metric keyway sizes are based on ISO standards – see catalog chart for a listing of the standard sizes.
Please Note: Bolted-Style Control-Flex Couplings utilize set-screw hubs with keyways. In this case, standard keyway sizes are based on AGMA standards, and the metric keyway sizes are based on ISO standards – see catalog chart for a listing of the standard sizes.
Schmidt Offset Coupling
How do I size a Schmidt Offset Coupling?
There is a selection procedure outlined in the Schmidt Coupling catalog available through the “Downloads” section of this website.This procedure factors in the amount of offset needed for the application (whether it is a fixed or variable offset), the horsepower and speed of the application, the bearing lifetime, and the hub bore size requirements in selecting the right Offset Coupling for a specified lifetime in the application.
The coupling specifications list a maximum torque capacity for the coupling; however, that is a static torque capacity and represents the strength of the coupling without concern for bearing lifetime.Sizing the coupling using the selection procedure outlined in the catalog will ensure the Offset Coupling selected will perform for the desired lifetime in the specified application.
Please call the factory with any questions or for assistance in selecting the right Offset Coupling for your application.
The coupling specifications list a maximum torque capacity for the coupling; however, that is a static torque capacity and represents the strength of the coupling without concern for bearing lifetime.Sizing the coupling using the selection procedure outlined in the catalog will ensure the Offset Coupling selected will perform for the desired lifetime in the specified application.
Please call the factory with any questions or for assistance in selecting the right Offset Coupling for your application.
Why can’t I operate my Schmidt Offset Coupling at zero parallel misalignment or at its full parallel misalignment rating?
The center disc of the Offset Coupling is supported by 3 or more links on either side, which allows for its large misalignment range.Within the allowable offset range, the angle between these links defines the position of the center disc and provides proper support and stability for it.As you approach zero parallel misalignment, or to the Offset Coupling’s full parallel misalignment rating, the angle between the links is compromised, they do not properly support the center disc, and reaction loads on the connected components are greatly increased in this condition.Strict adherence to the minimum and maximum parallel misalignment ratings listed in the catalog will ensure smooth operation of the Offset Coupling without inducing any sideloads or reaction loads on the connected components.
What is the difference between the L100, L200, and L300 series of Schmidt Offset Couplings?
Each of these series of Offset Couplings is constructed differently to provide unique benefits for a particular application.For assistance with which coupling may be right for your application, please call or e-mail us at the factory.
- The L100 series uses oil-impregnated links generally used in light-duty applications having smaller torque values, smaller shaft diameters, and smaller amounts of parallel offset.
- The L200 series uses rolling element needle bearings with steel links.This coupling will handle much larger torque capacities and provide long life in industrial applications.This coupling may be re-lubricated over its lifetime and offers a high horsepower/torque capacity along with moderate speed and moderate parallel offset capability.
- The L300 series uses rolling element needle bearings with aluminum links.These longer aluminum links provide higher speed capacity, higher amounts of parallel offset, and offer a moderate torque capacity in comparison to the L200 series.
Does the Schmidt Offset Coupling apply reaction loads on the connected components?
No. The Offset Coupling does not impart any reaction loads or sideloads on the connected components, provided it is operated within the minimum and maximum parallel offset limits listed in the catalog.The multiple links in the Offset Coupling design balance the torque forces so no reaction loads are present in the application.The only sideload to be accounted for would be the weight of the coupling itself.
What is the backlash amount in the Schmidt Offset Coupling?
The standard L200 and L300 series offer 0.010” – 0.015” of radial play at the outside diameter of the Offset Coupling.This radial play is needed for bearing clearances internal to the coupling.The same amount of radial play pertains to any size Offset Coupling, so larger diameter Offset Couplings will then have less angular rotational backlash than smaller Offset Couplings.
If greater precision is required, we do offer a “Low Backlash” version which reduces the backlash value to 0.003” - 0.005” at the outside diameter of the coupling as well as an “Ultra-Low Backlash” version which reduces the backlash value to 0.002” - 0.003” at the outside diameter of the coupling.These special versions must be specified.If greater precision is required, or to discuss your specific requirements, please contact the factory for a detailed application review.
If greater precision is required, we do offer a “Low Backlash” version which reduces the backlash value to 0.003” - 0.005” at the outside diameter of the coupling as well as an “Ultra-Low Backlash” version which reduces the backlash value to 0.002” - 0.003” at the outside diameter of the coupling.These special versions must be specified.If greater precision is required, or to discuss your specific requirements, please contact the factory for a detailed application review.
- Please Note:The L100 series does not have as low backlash as the L200 and L300 series and is generally not recommended for use in high precision applications.
What is the expected lifetime of a Schmidt Offset Coupling?
Lifetime of a Schmidt Offset Coupling is typically described in L10 hours.When the Offset Coupling is sized and selected for an application, a design lifetime is used for the selection.Provided the next smaller or larger coupling will provide an acceptable offset range for the application:
- Going smaller in size from the selected coupling will result in reduced lifetime.
- Going larger in size from the selected coupling will result in increased lifetime.
What are the standard keyway sizes?
The standard keyway sizes are based on AGMA standards, and the metric keyway sizes are based on ISO standards – see catalog chart for a listing of the standard sizes.
Do I need to lubricate my Schmidt Offset Coupling?
Yes. The L200 and L300 series utilize needle bearings and do require periodic re-lubrication with grease. Both the L200 and L300 series couplings have a low-profile grease fitting that is compatible with an Alemite Z-737 adaptor for a grease gun. The frequency of re-lubrication can vary based on the coupling used as well as the operating speed of the coupling. See the Instruction Sheet for your Schmidt Offset Coupling part number for more details. The Instruction Sheets can be found under the “Downloads” section of this website.
- Please Note:The L100 series couplings utilize oil impregnated links, and no re-lubrication is required.However, periodically adding a drop of oil to each link may help to extend lifetime.
Schmidt Inline Couplings
How do I size a Schmidt Inline Coupling?
There is a selection procedure outlined for the Inline Coupling in the Schmidt Coupling catalog available through the “Downloads” section of this website.This procedure factors in the horsepower and speed of the application and applies a service factor to the resulting torque to obtain a design torque for the selection process.Please call the factory with any questions or for assistance in selecting the right Inline Coupling for your application.
What is the backlash amount in the Schmidt Inline Coupling?
The standard L400 series Inline Couplings offer 0.010” – 0.015” of radial play at the outside diameter of the Inline Coupling.This radial play is needed for bearing clearances internal to the coupling.The same amount radial play pertains to any size Inline Coupling, so larger diameter Inline Couplings will then have less angular rotational backlash than smaller Inline Couplings.
If greater precision is required, we do offer a “Low Backlash” version which reduces the backlash value to 0.003” - 0.005” at the outside diameter of the coupling as well as an “Ultra-Low Backlash” version which reduces the backlash value to 0.002” - 0.003” at the outside diameter of the coupling.These special versions must be specified.If greater precision is required, or to discuss your specific requirements, please contact the factory for a detailed application review.
If greater precision is required, we do offer a “Low Backlash” version which reduces the backlash value to 0.003” - 0.005” at the outside diameter of the coupling as well as an “Ultra-Low Backlash” version which reduces the backlash value to 0.002” - 0.003” at the outside diameter of the coupling.These special versions must be specified.If greater precision is required, or to discuss your specific requirements, please contact the factory for a detailed application review.
What is the expected lifetime of a Schmidt Inline Coupling?
Since the bearings in the Inline Coupling design swivel, rather than fully rotate in the coupling, bearing lifetime is greatly increased and generally not an issue. Due to this unique type of service the bearings see during operation, we do not have a lifetime calculation available.
What are the standard key sizes?
The standard keyway sizes are based on AGMA standards, and the metric keyway sizes are based on ISO standards – see catalog chart for a listing of the standard sizes.
Do I need to lubricate my Schmidt Inline Coupling?
Yes. The L400C series have needle bearings and do require periodic re-lubrication with grease. The frequency of re-lubrication can vary based on the coupling used as well as the operating speed of the coupling. See the Instruction Sheet for your Schmidt Inline Coupling part number for more details. The Instruction Sheets can be found under the “Downloads” section of this website.
- Please Note: We do offer a special L400D series that use Duralon bearings that do not require relubrication. Please contact the factory if you are interested in this bearing option
Schmidt 5-D Couplings
How do I size a Schmidt 5-D Coupling?
There is a selection procedure for the 5-D Coupling outlined in the Schmidt Coupling catalog available through the “Downloads” section of this website. This procedure factors in the horsepower and speed of the application and applies a service factor to the resulting torque to obtain a design torque for the selection process. Please call the factory with any questions or for assistance in selecting the right Inline Coupling for your application.
What is the backlash amount in the Schmidt 5-D Coupling?
The standard L500 series 5-D Couplings offer 0.010” – 0.015” of radial play at the outside diameter of the coupling. This radial play is needed for bearing clearances internal to the coupling. The same amount radial play pertains to any size of 5-D Coupling, so larger diameter 5-D Couplings will then have less angular rotational backlash than smaller 5-D Couplings. Due to the bearing style used in this coupling, reduced backlash options are not available.
What is the expected lifetime of a Schmidt 5-D Coupling?
Since the bearings in the 5-D Coupling design swivel, rather than fully rotate in the coupling, bearing lifetime is greatly increased and generally not an issue. Due to this unique type of service the bearings see during operation, we do not have a lifetime calculation available.
What are the standard keyway sizes?
The standard keyway sizes are based on AGMA standards, and the metric keyway sizes are based on ISO standards – see catalog chart for a listing of the standard sizes.
Do I need to lubricate my 5-D Coupling?
Yes. The 500S series couplings do require periodic re-lubrication with grease. The frequency of re-lubrication can vary based on the coupling used as well as the operating speed of the coupling. See the Instruction Sheet for your Schmidt 5-D Coupling part number for more details. The Instruction Sheets can be found under the “Downloads” section of this website.
Overhung Load Adaptors
Overhung Load Adaptors (OHLA®)
What is the load rating for the Overhung Load Adaptors (OHLA)?
Although some references use an Overhung Load Rating to determine selection for an application, this is a static rating which neglects many factors that influence the lifetime of the unit. Zero-Max uses a combination of dynamic load rating (bearing life estimate based on application details) and over 40-years of industry-leading experience to determine the fit for an application. Strength of the input connection should also be considered in OHLA selection.
The estimated life calculation can be done by the factory with some basic application information including:
It is recommended to contact Zero-Max with your application specifications so an accurate L10h bearing life and input connection strength can be evaluated. Zero-Max Engineering can offer customization options to improve OHLA life expectancy in many applications if a standard unit will not suffice.
The estimated life calculation can be done by the factory with some basic application information including:
- HP
- Speed (rpm)
- Type of load – fan, blower, pulley, etc.
- If a pulley, the diameter of the pulley and the distance from the face of the OHLAs output pilot are critical
- If an axial fan, the fan weight, and the amount of thrust load are critical. If the thrust load is not known, this can be calculated if the diameter of the fan, the CFM air flow, and the static pressure are provided.
- Mounting Orientation (horizontal; vertical, shaft-up, or vertical, shaft-down)
- Hydraulic motor/pump part number and/or a catalog page for the motor/pump
It is recommended to contact Zero-Max with your application specifications so an accurate L10h bearing life and input connection strength can be evaluated. Zero-Max Engineering can offer customization options to improve OHLA life expectancy in many applications if a standard unit will not suffice.
What are the recommended lubrication methods?
Grease Lubrication is considered standard and is the preferred method for the vast majority of our OHLA applications. With grease, there is little or no leakage concerns, low maintenance, and it provides acceptable life in most applications. Unique applications and/or personal preference may drive the use of static oil or circulating oil flow-thru lubrication instead. Please contact the factory in these instances as often slight modifications to the OHLA housing must be done to provide for this.
Applying grease to the spline teeth on the motor or pump shaft is also recommended at the time of installation. If a keyed motor or pump shaft is used, it is also a good idea to add grease to the motor or pump shaft and key at the time of installation.
The amount and type of recommended grease is listed in the “OHLA Lubrication and Operation Guide” under the Downloads section of this web-site. It is important to follow these guidelines. Please ensure to avoid over-filling, as that can lead to problems as well. Following the OHLA Lubrication guidelines will offer best conditions for longer life. Contact the factory for further details.
Applying grease to the spline teeth on the motor or pump shaft is also recommended at the time of installation. If a keyed motor or pump shaft is used, it is also a good idea to add grease to the motor or pump shaft and key at the time of installation.
The amount and type of recommended grease is listed in the “OHLA Lubrication and Operation Guide” under the Downloads section of this web-site. It is important to follow these guidelines. Please ensure to avoid over-filling, as that can lead to problems as well. Following the OHLA Lubrication guidelines will offer best conditions for longer life. Contact the factory for further details.
Can the OHLA’s be mounted vertically or at an angle / incline?
Yes. However, standard OHLA units are configured for a horizontal mounting (shaft parallel with the ground). Applications requiring a vertical shaft mounting orientation, or that are mounted at an angle or incline, will require special features to retain lubricant in the uppermost bearing and may require additional modifications as well. These features vary depending on the model of the OHLA and the application’s operating parameters. Please contact factory for details if you have a vertical or inclined mounting orientation.
My OHLA is running hot, what temperature is permissible?
It is normal for an OHLA to run warm or perhaps even ‘hot’. Heat in the OHLA may be generated by the load, speed, lubrication method, and/or ambient temperature in the application. Running an OHLA with no load may also cause excessive heat. If you suspect your OHLA may be running excessively hot, you can use a temperature probe or infrared thermometer to check the operating temperature. Standard OHLA units are designed to operate between -40°F to +212°F (-40°C to +100°C). If your OHLA is running hotter, please contact the factory to discuss your application and the lubrication for the OHLA.
How do I identify my OHLA for replacement?
If your OHLA is a special, it will have a special part number stamped into one of the machined mounting pads at the base of the OHLA housing (see below). Special part numbers start with the letter ”L” and are followed by 6 numeric digits.
If no part number is stamped into either of the machined mounting pads at the base of the OHLA housing, you have a standard OHLA. Please call the factory or refer to the OHLA catalog to match up to the housing and shaft dimensions to the corresponding standard model part number.
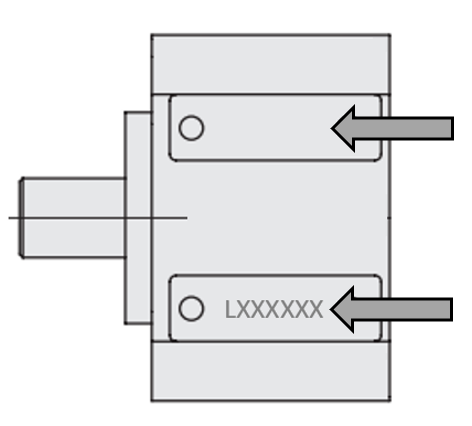
My pump or motor will not fit up to a standard OHLA, can Zero-Max make one to fit?
Yes. The standard OHLA product line is designed primarily for the most commonly used SAE hydraulic pump and motor mountings, in addition to a popular non-SAE mounting. Should you find the mounting needed for your application is not in the catalog, please contact Zero-Max to determine the necessary mounting requirements. Over half of the OHLAs we make are specials including those we modify to accommodate special mounting and/or shaft dimensions. Zero-Max can design transition adapters for DIN, ISO, IEC, NEMA, and other non-SAE requirements, as well as step-up or step-down adapters.
What if I have a challenging operating environment?
No Problem! All our standard OHLAs have been field-proven to survive in harsh environments. Zero-Max also manufactures heavier-duty models as well as special OHLAs when needed for an application. We have the expertise and experience necessary to guide you to the right selection. Our extensive knowledge of successfully utilizing a wide range of materials and coatings can assure long term protection and maximum value. Please contact us with your requirements to learn more.
Power Transmission Products
Torq-Tender® Overload Safety Devices
If I already have an electronic shear pin on the motor drive, do I still need a mechanical torque limiter?
An electronic shear pin is designed to sense excessive motor current, which would indicate an elevated torque load, and then react to shut down the motor. However, the motor is located at the beginning of the drive line and can be less sensitive to overloads downstream from the motor, due to torque multiplications from gear reductions and the inertia of the total driveline. Additionally, the motor may be driving multiple stations on the machine, making an electronic shear pin even less sensitive to an overload in any one station of the machine. In these instances, having a mechanical torque limiter, like the Torq-Tender, further down the driveline can provide a more accurate and faster response to a torque overload.
Where is the best location to place a Torq-Tender in my driveline?
Torq-Tenders should be installed as close to the item you want to protect in the driveline as possible. Locating the Torq-Tender away from the motor, further down the driveline, will provide a more accurate and faster response to an overload since the effects of any gear reductions or inertia are reduced.
Can either end of the Torq-Tender be the input or output (Driver or Driven)?
The Torq-Tender is designed for bidirectional operation, meaning it can be rotated or disengaged in either direction. As a result, either end can be the driver or driven end.
However, if using an Actuating Pin option, it is important the ‘Housing’ end of the Torq-Tender is connected to the driving side of the installation. The Actuating Pin is located in the Housing end of the Torq-Tender, and in the event of an overload, the Actuating Pin/Housing will then continue to rotate to contact a limit switch or sensing device in the installation.
For Actuating Disc models, either end may be the driving or driven end; however, care should be taken to ensure the Actuating Disc actuates toward the limit switch or sensing device in the installation.
However, if using an Actuating Pin option, it is important the ‘Housing’ end of the Torq-Tender is connected to the driving side of the installation. The Actuating Pin is located in the Housing end of the Torq-Tender, and in the event of an overload, the Actuating Pin/Housing will then continue to rotate to contact a limit switch or sensing device in the installation.
For Actuating Disc models, either end may be the driving or driven end; however, care should be taken to ensure the Actuating Disc actuates toward the limit switch or sensing device in the installation.
What if I am experiencing nuisance tripping (disengagement) of my Torq-Tender?
Nuisance tripping, especially in new installations, often means you are on the edge of the torque setting you need for your machine. Going to the next largest torque spring setting for your Torq-Tender may be all that is needed to correct the nuisance tripping. The torque setting may be increased by changing the internal springs – please see the Torq-Tender Assembly and Spring Change Instructions in the “Downloads” section of our website for more detail.
Other items to review if you are experiencing nuisance tripping are:
Other items to review if you are experiencing nuisance tripping are:
- Make sure the Torq-Tender is fully reset before restarting the machine. If the Torq-Tender drive key is not fully reset into its detented position, inertia of the machine may keep it from resetting upon start-up. It is always recommended to jog the motor forward or reverse (either direction is fine) to get the Torq-Tender to reset, or else manually counter-rotate both ends of the Torq-Tender relative to each other until reset. You should hear an audible “click” when the unit resets into its detented position.
- Soft-start the motor. If starting torque is causing the nuisance tripping, then using a soft-start on the motor will gradually accelerate the machine and lessen the amount of starting torque seen by the Torq-Tender, potentially resolving the nuisance tripping.
- Nuisance tripping after extended use may indicate either the springs need replacement, or the housing is potentially worn from excessive tripping.
Can an Actuating Pin or Actuating Disc be added in the field?
The Actuating Pin may be ordered factory installed on any Torq-Tender model. The Actuating Pin feature can be added in-the-field to Torq-Tender sizes TT3 and larger. Sizes TT2X and smaller require factory built-to-order units (cannot be added in the field), as do Actuating discs for all size Torq-Tenders.
How can I identify the torque setting in my Torq-Tender?
You may have documentation from the machine builder that identifies the torque setting. If not, the internal springs of the Torq-Tender are color-coded to identify the torque setting. A procedure for accessing the springs as well as a color code chart are included in the Torq-Tender Assembly and Spring Change Instructions located in the “Downloads” section of our website.
Can I change the torque setting in the field?
The torque setting may be increased or decreased by changing the internal springs – please see the Torq-Tender Assembly and Spring Change Instructions in the “Downloads” section of our website.
What is the maximum running speed for the Torq-Tender?
The Torq-Tender is designed for operation at speeds up to 1,800 rpm; however, the Torq-Tender performance may be affected by, and sensitive to, inertia in the system at higher speeds. Contact the factory for higher speed applications. It is also recommended to include an actuating pin or actuating disc at higher speeds for immediate shut down of the motor to prevent excessive overloads of the Torq-Tender.
Does the Torq-Tender have backlash?
Yes. Torq-Tenders will have a small amount (generally 1° - 1½°) of rotational backlash. This amount of backlash is typically acceptable in most Power Transmission applications.
Can the Torq-Tender be mounted vertically?
Yes. A vertical mounting arrangement is acceptable; however, the vertical shafts should be fully supported in bearings so the Torq-Tender does not have any axial thrust load applied to it.
What are the standard keyway sizes?
The standard keyway sizes are based on AGMA and ISO standards. Please refer to the Overload Safety Couplings Catalog for a table that lists all standard keyway sizes. Non-standard keyway sizes are also available. Please contact the factory for further details.
Can I get a Torq-Tender for washdown or other harsh environments?
Yes. The standard models of the Torq-Tender have a black oxide finish, which gives mild corrosion protection to stand up to most industrial environments. Where moisture, water spray, or other contaminants are present, special options are available including nickel plating, other plating, or stainless-steel versions. Additionally, o-ring seals may be added to the housing to help seal the Torq-Tender to protect it from water and other contaminants. Food Grade grease options are also available. Please contact the factory if any of these special features are needed for your application.
What happens if my Torq-Tender operates in an overload mode for an extended period of time?
The Torq-Tender is designed to protect against occasional overloads. Repeated overloads, or if the Torq-Tender is left to run continuously in an overloaded condition, will cause internal wear. The result of this wear can include torque setting drift, or a decrease in the trip torque from the original torque setting. If the machine is unattended or running at faster speeds, use of an Actuating Pin or Actuating Disc option is recommended to shut down the motor immediately in the event of an overload, preventing excess wear.
H-TLC Overload Safety Devices
If I already have an electronic shear pin on my motor drive, do I still need a mechanical torque limiter?
An electronic shear pin is designed to sense excessive motor current, which would indicate an elevated torque load, and then react to shut down the motor. However, the motor is located at the beginning of the drive line and can be less sensitive to overloads downstream from the motor, due to torque multiplications from gear reductions and the inertia of the total driveline. Additionally, the motor may be driving multiple stations on the machine, making an electronic shear pin even less sensitive to an overload in any one station of the machine. In these instances, having a mechanical torque limiter, like the H-TLC, further down the driveline can provide a more accurate and faster response to a torque overload.
Where is the best location to place an H-TLC in my driveline?
H-TLC units should be installed as close to the item you want to protect in the driveline as possible. Locating the H-TLC away from the motor, further down the driveline, will provide a more accurate and faster response to an overload since the effects of any gear reductions or inertia are reduced.
Can either end of the H-TLC be the input or output (Driver or Driven)?
The H-TLC is designed for bidirectional operation, meaning it can be rotated or disengaged in either direction. As a result, either end can be the driver or driven end.
If an Actuating Disc is being used, either end may still be the driving or driven end; however, care should be taken to ensure the Actuating Disc actuates toward the limit switch or sensing device in the installation.
If an Actuating Disc is being used, either end may still be the driving or driven end; however, care should be taken to ensure the Actuating Disc actuates toward the limit switch or sensing device in the installation.
What if I am experiencing nuisance tripping (disengagement) of my H-TLC?
Nuisance tripping, especially in new installations, often means you are on the edge of the torque setting you need for your machine. Increasing the torque setting of the H-TLC may be all that is needed to correct the nuisance tripping. Since the H-TLC is externally adjustable, tightening the torque adjustment screws will increase the torque setting. If you cannot get enough torque increase from the torque adjustment screws, you may need to consider going to the next larger spring set. Please see the H-TLC Assembly and Spring Change Instructions in the “Downloads” section of our website.
Other items to review if you are experiencing nuisance tripping are:
Other items to review if you are experiencing nuisance tripping are:
- Make sure the H-TLC is fully reset before restarting the machine. If the H-TLC is not fully reset into its detented position, inertia of the machine may keep it from resetting upon start-up. It is always recommended to jog the motor forward or reverse (either direction is fine) to get the H-TLC to reset, or else manually counter-rotate both ends of the H-TLC relative to each other until reset. You should hear an audible “click” when the unit resets into its detented position.
- Soft-start the motor. If starting torque is causing the nuisance tripping, then using a soft-start on the motor will gradually accelerate the machine and lessen the amount of starting torque seen by the H-TLC, potentially resolving the nuisance tripping.
- Nuisance tripping after extended use may indicate either the springs need replacement, or the housing is potentially worn from excessive tripping.
Can an Actuating Disc be added in the field?
Yes. The H-TLC may be ordered with the Actuating Disc already installed, or it may be added in the field. The Actuating Disc, along with a retaining ring and wave spring, are the components you would need to add. These components are available from the Zero-Max factory.
How can I identify the torque rating range in my H-TLC?
You may have documentation from the machine builder that identifies the torque setting.If not, the internal springs of the H-TLC are color-coded to identify the torque setting range. A procedure for accessing the springs as well as a color code chart are included in the H-TLC Assembly and Torque Adjustment Instructions located in the “Downloads” section of our website.
What is the maximum running speed for the H-TLC?
The H-TLC is designed for operation at speeds up to 1,800 rpm; however, the H-TLC performance may be affected by, and sensitive to, inertia in the system at higher speeds. Contact the factory for higher speed applications. It is also recommended to include an actuating disc at higher speeds for immediate shut down of the motor to prevent excessive overloads of the H-TLC.
Does the H-TLC have backlash?
Yes. The H-TLC will have a small amount (generally 1° - 2°) of rotational backlash. This amount of backlash is typically acceptable in most Power Transmission applications.
Can the H-TLC be mounted vertically?
Yes. A vertical mounting arrangement is acceptable; however, the vertical shafts should be fully supported in bearings so the H-TLC does not have any axial thrust load applied to it.
What are the standard keyway sizes?
The standard keyway sizes are based on AGMA and ISO standards.Please refer to the Overload Safety Couplings Catalog for a table that lists all standard keyway sizes.Non-standard keyway sizes are also available.Please contact the factory for further details.
Can I get an H-TLC to hold up to washdown and harsher environments?
Yes. The H-TLC is corrosion resistant in its standard form, having a composite exterior, with plated steel and stainless-steel hardware. If additional corrosion protection is needed, we can make a special unit, substituting all stainless-steel hardware on the exterior and even stainless-steel springs in the interior of the H-TLC. Food Grade grease options are also available. Please contact the factory if any of these special features are needed for your application.
What happens if my H-TLC operates in an overload mode for an extended period of time?
The H-TLC is designed to protect against occasional overloads. Repeated overloads, or if the H-TLC is left to run continuously in an overloaded condition, will cause internal wear. The result of this wear can include torque setting drift, or a decrease in the trip torque from the original torque setting. If the machine is unattended or running at faster speeds, use of the Disc option is recommended to shut down the motor immediately in the event of an overload, preventing excess wear.
Adjustable Speed Drives
What is the maximum output speed or output speed range?
The output speed range of all Zero-Max Drives is adjustable from 0 to ¼ of the input speed. In other words, the Drives offer a 4:1 ratio of the input to output speed, or inversely, a 0 to 0.25:1 ratio of the output speed to input speed.
What lifetime might I expect from my Zero-Max Drive?
When properly sized for an application, it is not uncommon for Zero-Max Drives to have an operating life of 15,000 to 20,000 hours or more. In addition to using a service factor when sizing, starting and accelerating the output load slowly or starting at zero speed and gradually increasing the output speed will minimize stress on the Drive and further extend lifetime. Shock loads or jam-ups on the connected equipment can create torque spikes and overloads that can shorten lifetime. If shock loads or overloads are anticipated in the application, use of a torque limiting device on the output of the Zero-Max Drive is recommended.
Can you change the output rotation on a Zero-Max Drive?
No. The output shaft rotation is driven by one-way clutches and cannot be changed. As a result, changing the input shaft direction will not change the output shaft direction. In the E and JK series (only) Zero-Max Drives, we do offer a reversing output version that has a special clutch and shifting mechanism to allow for reversing the output shaft direction.
Is the input shaft rotation direction critical?
Yes. All Zero-Max Drives have a preferred input rotation direction (see catalog) which should be chosen when possible. If your application requires the Drive to be run in the non-preferred input rotation direction, this is also acceptable; however, you may notice an increased output shaft speed, excess noise and/or vibration, and a slight life reduction of the unit. These effects are often lessened with lower input speeds. Contact Factory for more details.
Can I rebuild my Zero-Max Drive?
No. The Zero-Max Drive is not field serviceable.
Is it normal for my Drive to run hot?
The Zero-Max Drives will run hot to the touch. The temperature rise will be more pronounced on initial run-in, and then will decrease in temperature after a “break-in” period. Refer to the Zero-Max Drive Instructions for further details.
Does the Zero-Max Drive need to be relubricated?
No. The Zero-Max Drive is supplied filled with the appropriate level of oil. The case is sealed and has an adequate level of oil for any mounting orientation. If an oil leak is noted at some time in the life of the Drive, and you add additional oil to compensate for the leakage, take care not to fill the unit any higher than the centerline of the highest shaft in the installation. Adding oil beyond that level can cause excess pressure inside the case and may affect the performance of the unit and shaft seals.
Is there a recommended mounting orientation?
No. The most common mounting orientation is on a horizontal surface with the mounting feet secured to a flat surface; however, other mounting arrangements may be used. Other common mounting orientations include a wall mount with the Drive positioned vertically or mounting the Drive upside down.
Is the torque constant on the output shaft of the Zero-Max Drive?
Yes. The Zero-Max Drive provides constant torque throughout the speed range.
Crown Gear Right Angle Gearboxes
What is the backlash of a Crown Gear Drive?
The backlash in a standard Crown Gear Drive is ½°. Special units can offer a ¼° backlash value.¼° backlash is the lowest backlash offered in the Crown Gear Drive line.
What is the efficiency of the Crown Gear Drive?
The Crown Gear Drive uses high quality spiral bevel gears and ball bearings resulting in an efficiency of approximately 96%.
Can I reverse the relative rotation between the input and output shafts of the Crown Gear Drive?
- The 2-way Crown Gear Drive units offer the relative rotation between the 2 shafts as shown in the catalog. In some cases, the units with the opposite relative rotation can be built – contact the factory. A 3-way unit may be used in this case by either not connecting to the 3rd shaft or by removing it (at the factory or in the field).
- The 3-way Crown Gear Drive units are symmetrical along the axis of shaft #1 as shown in the catalog.By flipping the unit over along the shaft #1 axis, you can change the relative rotation between the input and output shafts using the same mounting locations.
Does the Crown Gear Drive need to be relubricated?
No. The Crown Gear Drives are grease-filled at the factory and do not require lubrication at the time of installation. Additionally, the grease is self-contained in the housing and does not require any relubrication for the life of the unit.
Is there a recommended mounting orientation?
No. Our standard Crown Gear Drives can be mounted in any orientation. Additionally, each standard unit can be secured using either the (3) housing mounting holes against a flat surface, or with the mounting flange holes provied at each input/output shaft location. Refer to catalog for mounting hole dimensioning.
Where should I use the IP-65 Rated Crown Gear Drives?
The IP-65 Rated Crown Gear Drives have shaft seals that protect against dust and water infiltration into the inside of the Crown Gear unit.These units are dust-tight and protected against water jets from any angle. These units also have a nickel-plated housing to provide corrosion resistance.The IP65 Crown Gear Drives are of benefit in any application where Ingress Protection and/or corrosion resistance is desired.
Can the Crown Gear Drives be submerged under water?
No. Our standard Crown Gear Drives are not rated for under water applications. However, we have manufactured special versions that allowed them to be used underwater in very specific applications. Contact the factory for further details.
Roh'lix® Linear Actuators
What is the “Lead” on the Roh’lix Actuator?
Lead refers to the linear distance traveled by the Roh’Lix block per one complete shaft revolution.A Right-Hand Lead is standard and is analogous to the motion of right-hand thread in a bolt and nut.The difference is the Roh’lix does not have threads and it offers overload protection.
Can I get a Left-Hand Lead on the Roh’lix Actuator?
Yes. Left-Hand leads are available, as are custom leads.The catalog lists the standard Right-Hand Lead units; however, both Right-Hand and Left-Hand Leads are available from a minimum of 0.025” (0.635mm) to a maximum of 3-times the shaft diameter.
What is the accuracy of the Roh’lix Actuator?
The Roh’lix is a friction device and as a result will show an accumulated error that in general is up to 0.002” per shaft revolution.Where greater accuracy is required, linear encoders can be used to indicate position.
What type of shafting should I use with the Roh’lix Actuator?
The recommended shaft material is C-1060 case-hardened and ground shafting, with a minimum hardness of 58 HRC.Its hardness will provide optimum life expectancy and its ground surface provides a uniform friction surface.Stainless Steel shafting, although slightly softer, is adequate for many applications requiring corrosion protection.
What kind of operating environments are suitable for the Roh’lix Actuator?
The Roh’lix relies on friction between the bearings and shaft to operate.Water, oil mist or grease can affect that performance.If water, oil, or grease are present, you may need to shield the Roh’lix or include a bellows cover to protect the Roh’lix from these items.Without water, oil, or grease present, any dirt or debris will not tend to stick to the shaft, and the split-block of the Roh’lix can allow it to ride over most debris that could get trapped in the way.In extreme applications a “shaft wiper” can be used in front of the Roh’Lix movement.
Can I get a stainless-steel version of the Roh’lix Actuator?
Yes. Stainless steel versions are available as a custom unit. Depending on the environment and application needs, the block of the Roh’lix is aluminum, and sometimes just stainless-steel bearings and hardware is all that is needed. Nickel plating and a clear chromate coating of the Roh’Lix block are two other methods for corrosion protection that are available upon request.
Can the Roh’lix Actuator be used in a vertical application?
Yes. A vertical load can cause the Roh’lix to back-drive or make the shaft spin backwards and allow the load to slowly drop down. Use of friction built into the slide or rotating shaft may be needed to eliminate back-driving or the use of a brake can also help.
How do I maximize the lifetime of the Roh’lix Actuator?
The minimum lifetime of the Roh’lix is 2-million inches of linear travel, based on testing.In the field, we have applications that have run more than 100-million inches of travel for lifetime.
To maximize lifetime, consider:
To maximize lifetime, consider:
- Thrust – Proper adjustment of the thrust adjustment screws will extend lifetime. Roh’lix lifetime is also increased when the application load is a smaller percentage of the unit’s thrust rating. Selecting an oversized Roh’lix is advisable to achieve the greatest lifetime of the unit.
- Lead/Shaft Speed – higher lead units will produce longer lifetime because fewer bearing revolutions will be required to move the same linear distance. Also, the reduction in driveshaft rpm will increase lifetime.
- Overloading – Occasional overload for short periods of time is acceptable. However, frequent or extended periods of overload and slippage will reduce lifetime.
- Sideloads/Twisting Loads – Minimizing sideloads and twisting loads will maximize life from the Roh’lix.
Is the Roh’lix Actuator repairable?
Yes. Bearing Assembly Kits are available from Zero-Max, which consist of all the bearings, bearing washers, and bearing mounting screws needed to rebuild one complete Roh’lix unit. We recommend using Zero-Max replacement bearings as they contain a specified grease and percentage of fill that has shown to work best with the Roh’lix. Use of commercially available bearings can create performance issues with the Roh’lix.
Is there required maintenance for the Roh’lix Actuator?
No. Although no regular maintenance is required for the Roh’lix Actuators, periodic inspection for signs of wear of the bearings and an occasional wiping of the Roh’lix shaft to remove any accumulated oil or debris can help ensure optimal performance and a long lifetime.
Phas-Lok Adjusting Hubs
Are other sizes/configurations of the Phas-Lok available?
Yes. Zero-Max can make custom bore sizes and/or custom features as needed for specific applications. We also make larger sized Phas-Lok hubs for applications requiring larger shaft sizes and higher torque values than shown in the catalog.
What features do I need to machine into my sprocket or other component for mounting to the Phas-Lok?
You will need to machine a bolt pattern with clearance holes to match the bolt pattern of the Phas-Lok. You will also need to add a bore to provide clearance for the hub pilot diameter. Please reference the Phas-Lok Installation Instructions, which may be found under the “Downloads” section of our website, for further details.
Can I get a machined and mounted sprocket on my Phas-Lok?
Yes. Please contact the factory with the model number of the sprocket or other component you would like mounted to the Phas-Lok. Zero-Max can then quote a complete Phas-Lok unit that includes the component machined-to-fit and mounted to the Phas-Lok.
Keyless Bushings
ETP® Connections
Can I use the ETP over an empty keyway?
No. The ETP should not be used overtop of an empty keyway, flats, or any other voids in the shaft surface. The hydraulic pressure internal to the ETP when mounted will cause the ETP sleeve to deform into the empty space and the connection will be compromised. If your shaft has an empty keyway, one option is to us a half key, having a rounded top to conform to the rounded shaft diameter. Another option may be to use a 2-part epoxy to fill the keyway, as long it conforms to the rounded shaft diameter.
What are the allowable radial and bending loads for my ETP?
Due to its hydraulic mounting principle, the ETP does have a limit on the allowable radial load and bending moment that may be applied to it. The ETP is designed for long service life when operated within these limits. These specifications are model and size dependent. Please refer to the limits listed in the ETP Catalog for specifications on your particular size ETP.
Are Diameter and Length of the shaft and hub critical with the ETP?
Yes. The entire ETP bushing ID should have contact with the shaft and the hub should engage the full length of the ETP bushing sleeve OD (up to the flange of the bushing). Additionally, the hub should have a sufficient thickness to properly mount to the ETP. Shaft tolerance and the hub bore tolerance are also important for proper operation and torque transmission. See the ETP catalog in the “Downloads” section of our web-site for details on proper hub sizing and dimensional/tolerance specifications for your particular size ETP.
Can I modify the bore or outer diameter of the ETP?
No. The ETP is constructed using thin-wall sleeves, so any modifications to these dimensions may damage the ETP or compromise its performance. If you have dimensional challenges in your application, please contact the factory to discuss options for a custom solution.
What if I have oil mist or oil/grease exposure in my application?
In most applications, if the mounting surfaces on the shaft, ETP, and hub bore are clean and free of oil or grease at the time of installation, having oil or grease present in the operating environment is not an issue. The ETP’s high contact pressure at the shaft and hub seal out any oil or grease, eliminating any migration of oil or grease into the connection areas.
Should I use an ETP or a PSL for my application?
The ETP has the advantage of faster and easier mounting and dismantling (less fasteners), more precise positioning (no axial movement during installation), excellent concentricity (hydraulic design). The ETP is generally the right choice when fast, frequent, and/or ultra-precise concentricity are required for your application.
The PSL is a more economical choice that provides higher radial load capacity. The PSL is also available in flangeless designs and for smaller shaft sizes. The PSL is generally the right choice if you will have infrequent changeout/repositioning needs or do not need exact axial positioning.
Both series are available in multiple models and materials as well as both metric and English sizes. Please contact the factory for any questions you may have on which model to use for your application.
The PSL is a more economical choice that provides higher radial load capacity. The PSL is also available in flangeless designs and for smaller shaft sizes. The PSL is generally the right choice if you will have infrequent changeout/repositioning needs or do not need exact axial positioning.
Both series are available in multiple models and materials as well as both metric and English sizes. Please contact the factory for any questions you may have on which model to use for your application.
How do I choose which ETP to use for my application?
Depending on the application requirements, one ETP model may be better suited for your specific application as compared to another. Some key features to consider are:
Download the ETP catalog for more details or contact the factory for assistance in choosing the optimal ETP for your application.
- Number and orientation of mounting screws
- Concentricity and runout specifications
- Torque and Radial load capacity
- Material options (alloy steel, stainless-steel)
- Number of mountings/dismantles required
Download the ETP catalog for more details or contact the factory for assistance in choosing the optimal ETP for your application.
Can the ETP be used in corrosive, washdown, or Food Grade environments?
Yes. ETP connections are available in alloy steel and stainless-steel in select models. This variety allows you to select an ETP model appropriate for your application. Unlike mechanical bushings, ETP bushings do not have slots for mounting which allow it to seal out the corrosive elements and contaminants in the bore area. Combined with the high contact pressure of the ETP, this feature allows the bushings to seal the mounting area, eliminating bacteria traps and making for an easier removal for any required maintenance. The clean design of stainless-steel ETP connections is great for Food Grade applications, and the ETP-Express-R stainless-steel model specifically includes an H1 Food Grade Grease for its pressure medium.
Posi-Lok®
Can I use the PSL over an empty keyway?
Yes. The mechanical shaft locking design of the PSL does allow for it to be mounted over an empty keyway. In this case, the torque rating of the PSL may be slightly reduced due to the loss of surface area; however, this difference is generally not significant enough to affect the application.
Does the PSL interchange with other brands of keyless shaft locking devices?
The PSL-G is interchangeable with a number of other suppliers bushings and is offered with competitive price and delivery. Other models of the PSL will have more limited interchanges; however, can often serve as substitutes in applications with flexible designs.
Are the Diameter and Length of the shaft and hub critical with the PSL?
Yes. The entire PSL bushing ID should have contact with the shaft and the hub should engage the full length of the PSL sleeve OD for full transmittable torque and the best concentricity. In the case of the PSL-K series, the engagement on the OD of the bushing sleeve is the full length, up to the flange of the bushing. Additionally, the hub should have a sufficient thickness to properly mount to the PSL. Shaft tolerance and the hub bore tolerance are also important for proper operation and torque transmission. See the Posi-Lok catalog in the “Downloads” section of our web-site for details on proper hub sizing and dimensional/tolerance specifications for your particular size PSL.
Should I use a PSL or an ETP for my application?
The PSL is a more economical choice that provides higher radial load capacity. The PSL is also available in flangeless designs and for smaller shaft sizes. The PSL is generally the right choice if you will have infrequent changeout/repositioning needs or do not need exact axial positioning.
The ETP has the advantage of faster and easier mounting and dismantling (less fasteners), more precise positioning (no axial movement during installation), excellent concentricity (hydraulic design). The ETP is generally the right choice when fast, frequent, and/or ultra-precise concentricity are required for your application.
Both series are available in multiple models and materials as well as both metric and English sizes. Please contact the factory for any questions you may have on which model to use for your application.
The ETP has the advantage of faster and easier mounting and dismantling (less fasteners), more precise positioning (no axial movement during installation), excellent concentricity (hydraulic design). The ETP is generally the right choice when fast, frequent, and/or ultra-precise concentricity are required for your application.
Both series are available in multiple models and materials as well as both metric and English sizes. Please contact the factory for any questions you may have on which model to use for your application.
How do I choose which PSL to use for my application?
Depending on the application requirements and available space, one PSL model may be better suited for your specific application as compared to another. Some key features to consider are:
Download the PSL catalog for more details or contact the factory for assistance in choosing the optimal PSL for your application.
- Flanged or Flangeless Design
- Torque Capacity
- Sizes available – small, large, english, metric
- Material options (steel, nickel-plated, stainless-steel)
- Contact pressure / hub size requirements
Download the PSL catalog for more details or contact the factory for assistance in choosing the optimal PSL for your application.
Can the PSL be used in corrosive, washdown, or Food Grade environments?
Yes. PSL bushings are available in alloy steel, nickel-plated, and stainless-steel in select models. This variety allows you to select a PSL model appropriate for your application. While the nickel-plated and stainless-steel PSL keyless bushings can hold up to corrosive environments, they may be limited in Food Grade applications due to the slotted design for mounting. In critical Food Grade applications, the ETP stainless steel models may be a better alternative.
Locate your nearest sales representative, request a quote, or contact us for all your application requirements.
- Home
- Contact Us
- Request Quote
-
FLEXIBLE SHAFT
COUPLINGS -
OVERHUNG LOAD
ADAPTORS -
POWER TRANSMISSION
PRODUCTS -
KEYLESS SHAFT
BUSHINGS -
INDUSTRIES
AND APPLICATIONS- Agriculture Equipment
- Automation Machines
- Beverage and Can Industry
- Fans and Blowers
- Dynamometer and Test Machinery
- Electrification
- Forestry Equipment
- Materials Handling
- Machine Tools
- Packaging Machinery
- Printing & Converting Industry Couplings
- Road Construction
- Specialty Machines
- Wind Turbine Couplings & Driveline Products
-
TECHNICAL
RESOURCES - DOWNLOADS
- About Us
- Representatives
- Standard Terms and Conditions
- Sitemap